Concrete admixtures play a crucial role in modern construction. These substances enhance concrete properties like strength, durability, and workability. However, improper use can lead to costly issues. This article highlights five common mistakes during admixture application and offers practical solutions to avoid them.
- Overadding Admixtures: Ignoring Dosage Guidelines
One frequent error is exceeding the recommended admixture dosage. Contractors may think more admixture means better performance. But excessive amounts can harm concrete properties. For example, too much water – reducing admixture can cause delayed setting or even concrete failure.
The root cause is often a lack of precise measurement. Some workers rely on guesswork instead of weighing admixtures accurately. This negligence disrupts the chemical balance in concrete, leading to inconsistent quality.
To solve this, always follow the manufacturer’s dosage instructions. Use calibrated equipment for measurement. Train workers to understand that admixture performance isn’t linear; optimal results come from specific ratios. Regularly check mixing records to ensure dosages stay within recommended ranges.
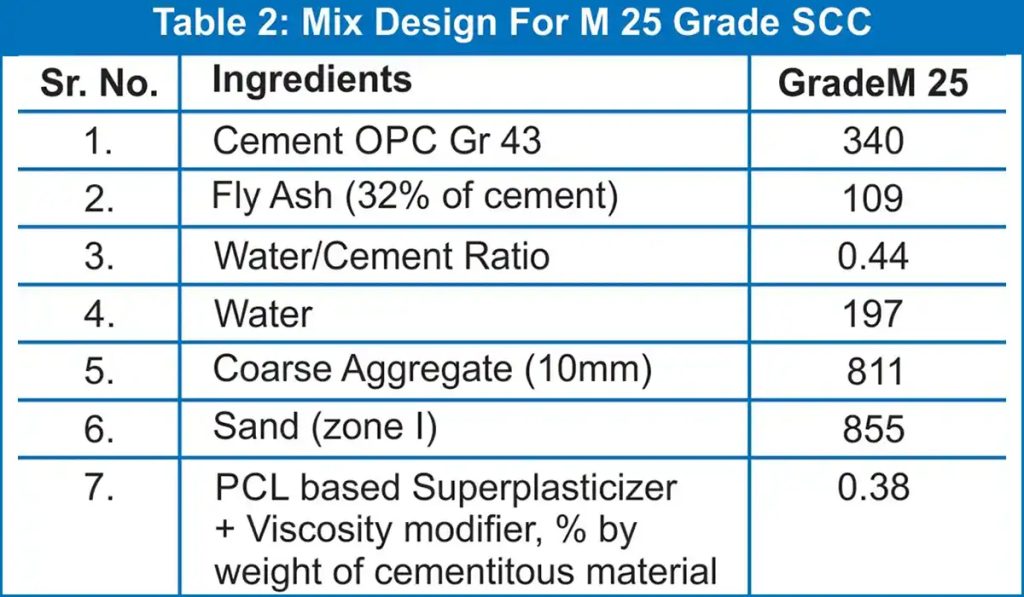
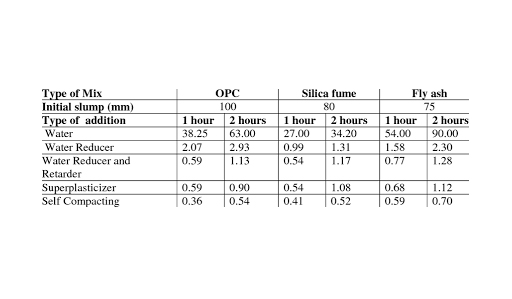
- Improper Mixing Sequence: Disregarding Addition Order
Many contractors add admixtures at the wrong stage of mixing. They might introduce them with dry materials or too late in the process. This mistake reduces admixture effectiveness, as poor dispersion leads to uneven distribution in the concrete mix.
The mixing sequence matters because admixtures interact differently with wet and dry components. Adding water – reducing admixtures with dry cement, for instance, can cause clumping instead of proper hydration. Timing errors also affect workability, making the mix harder to place.
To avoid this, follow the manufacturer’s recommended addition order. Most admixtures work best when added after the main ingredients are partially mixed. For example, add water first, then aggregates and cement, and introduce admixtures during the final mixing stage. This ensures uniform dispersion and maximizes their performance.
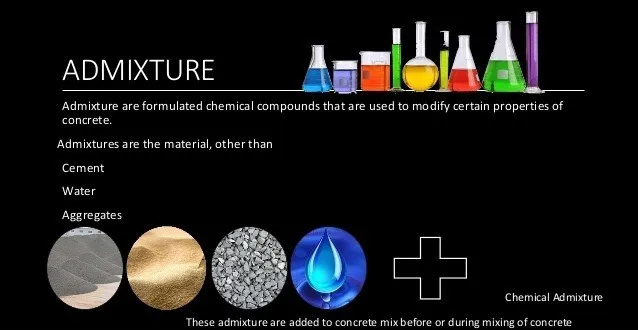
- Neglecting Compatibility Testing: Assuming All Admixtures Work Together
Using multiple admixtures without checking compatibility is a risky mistake. Different products may have conflicting chemical compositions. For example, combining certain air – entraining agents with superplasticizers can cause excessive foam or reduced strength.
Contractors often skip compatibility tests to save time or costs. But this oversight leads to issues like delayed setting, decreased durability, or even structural weaknesses. The problem is more common in complex mixes with multiple admixtures for specific properties.
The solution is to always test admixture combinations before large – scale use. Conduct trial mixes in the lab to observe reactions. Consult with admixture suppliers or engineers to ensure products are compatible. Document test results to create a reliable mixing formula for future projects. - Poor Storage Practices: Mishandling Admixture Shelf Life
Incorrect storage can degrade admixtures, reducing their effectiveness. Contractors may store them in unlabeled containers, expose them to extreme temperatures, or use expired products. Moisture contamination, especially for powdered admixtures, is another common issue.
Admixtures have specific storage requirements. Liquid admixtures can freeze or separate in cold temperatures, while heat can accelerate chemical breakdown. Expired products lose potency, and unlabeled containers lead to incorrect usage, such as using a water – reducing admixture instead of a setting accelerator.
To fix this, store admixtures in their original containers with clear labels. Follow manufacturer guidelines for temperature and humidity. Regularly check expiration dates and rotate stock to use older products first. Keep powdered admixtures in dry, sealed containers to prevent moisture absorption. - Ignoring Timing of Admixture Addition: Missing the Optimal Window
Adding admixtures too early or too late in the mixing process is a common oversight. Early addition might cause premature reactions, while late addition can prevent proper dispersion. Both issues affect concrete performance, such as reducing the expected slump or strength gain.
Workers often rush the process, not realizing that timing impacts admixture efficiency. For example, retarding admixtures need to be added when mixing starts to control setting time, while some accelerators work best when added with the final water portion.
The key is to understand each admixture’s purpose and timing requirements. Follow a strict mixing schedule that includes the exact stage for adding each admixture. Use timers or checklists to ensure consistency. Train crew members on the importance of timing in achieving the desired concrete properties.
Zaključak
Avoiding these common mistakes is essential for maximizing the benefits of concrete admixtures. Proper dosage, correct mixing sequence, compatibility testing, good storage practices, and timely addition are all critical. By following manufacturer guidelines, conducting tests, and training workers, contractors can prevent costly errors and ensure high – quality concrete in every project.
Remember, each admixture is a tool with specific uses. Treating them with care and precision not only improves concrete performance but also enhances the durability and safety of the structures we build. Stay informed about the latest industry standards and always prioritize best practices in admixture application.
Naš profesionalni tehnički tim dostupan je 24/7 za rješavanje svih problema s kojima se možete susresti dok koristite naše proizvode. Radujemo se vašoj suradnji!