The impressive performance of polycarboxylate superplasticizer powder boils down to its clever molecular design. Imagine a long polymer backbone with numerous shorter, negatively charged side chains sprouting off it. This unique architecture is key. The long chains physically push cement particles apart (steric hindrance), while the charged side chains (often carboxylates) attract water molecules, creating a repulsive force between particles. Engineers can fine-tune the ratio of backbone to side chains and the overall molecular weight of the polymer to perfectly match different concrete mixes, balancing flowability, strength development, and preventing the mix from becoming too thick.
So, how does this powder transform wet concrete? Cement particles naturally clump together due to weak attractive forces. The polycarboxylate molecules latch onto these particles, breaking up the clumps. This releases trapped water, instantly boosting workability. The charged groups then push particles apart electrostatically, while the extended side chains act like tiny spacers. This powerful combination—physical separation and electrical repulsion—significantly reduces friction between particles. The result is a more uniform mix where water is better retained, preventing the aggregates from separating and ensuring the concrete flows easily yet remains stable.
This efficient dispersion unlocks a major benefit: significant water reduction. Polycarboxylate powders typically allow for 20–40% less water compared to older plasticizers. This directly translates to a lower water-to-cement ratio, which is absolutely critical for concrete strength and durability. Less water means a denser structure forms as the cement hydrates. This denser matrix is much harder for damaging substances like deicing salts or chemicals to penetrate and significantly improves resistance to freeze-thaw damage. Furthermore, the excellent dispersion makes it easier to incorporate supplementary materials like fly ash or slag, allowing for more sustainable concrete without compromising performance.
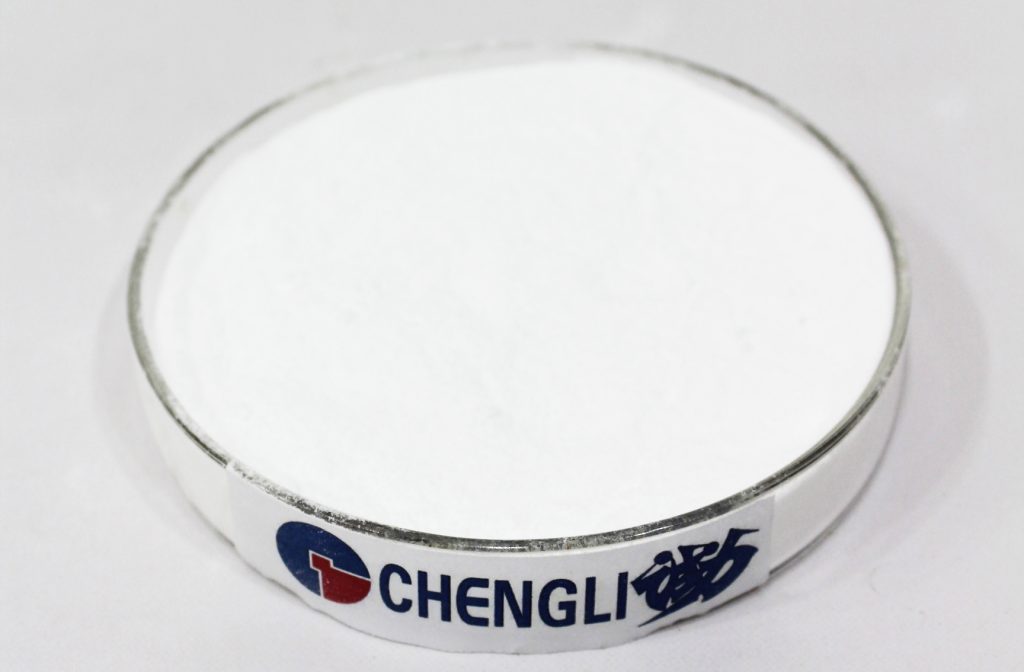
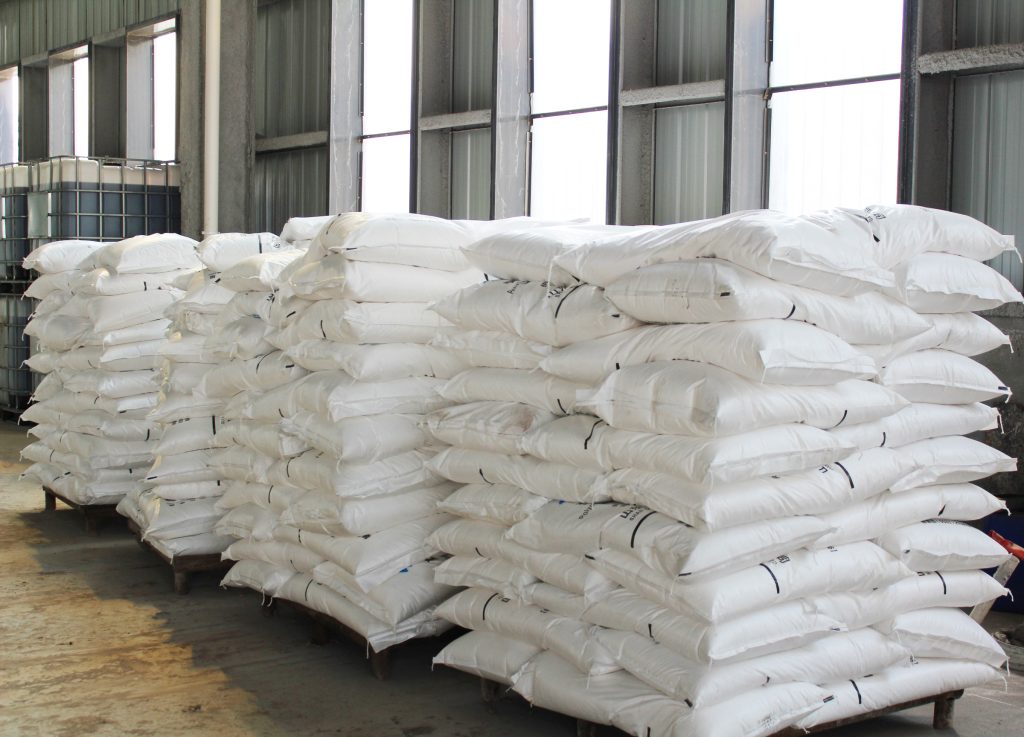
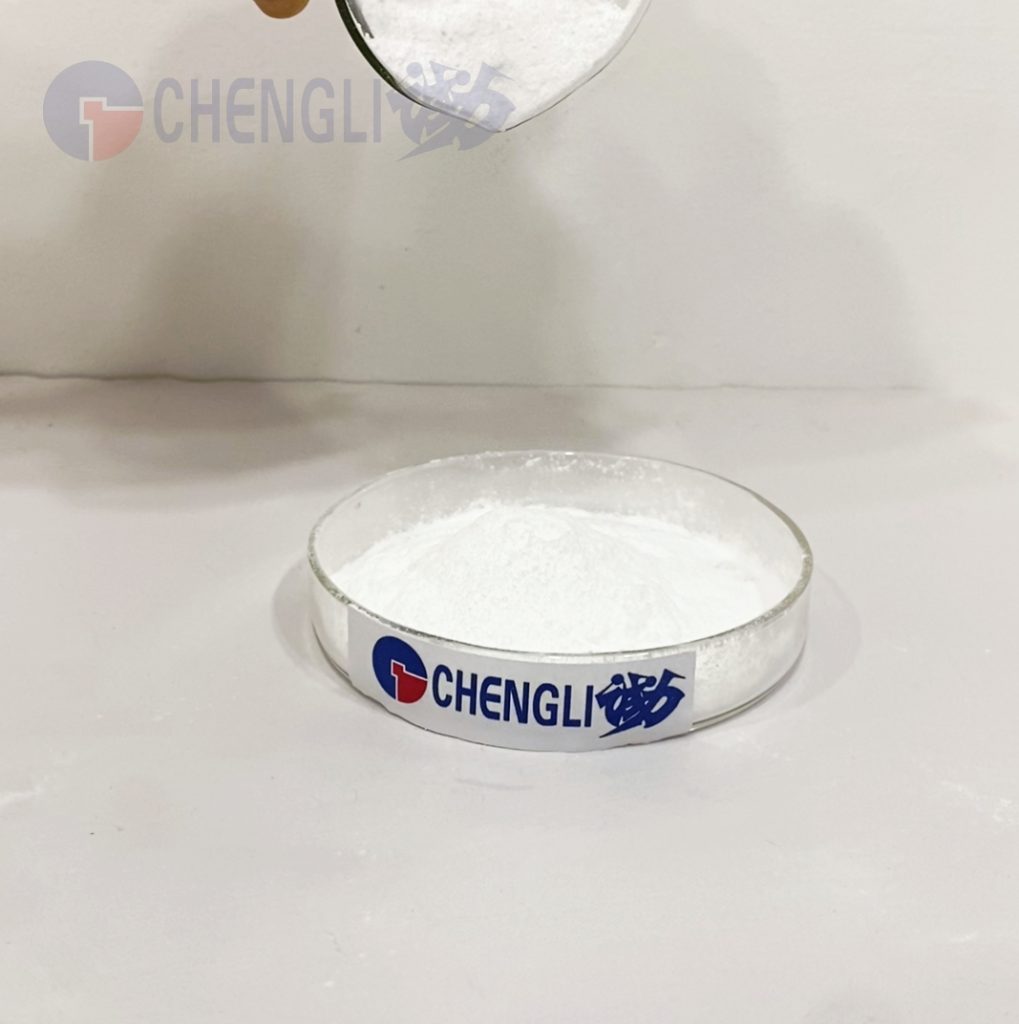
Why use powder instead of liquid? Stability is a big factor. The powder form boasts a longer shelf life, resisting bacterial growth and chemical breakdown far better than liquids during storage. It’s also more efficient to transport and handle – lighter, less bulky, and cheaper to ship. On the job site, the powder mixes directly with dry ingredients, avoiding potential errors in measuring liquids. Workers can precisely adjust the dosage batch-by-batch based on specific needs, reducing waste and ensuring consistent results even as temperature or humidity changes.
The interaction with cement hydration is fascinating. These superplasticizers don’t stop hydration; they manage its timing. Initially, the molecules coating the cement particles slightly slow down the reaction, giving workers more time to place the concrete. As hydration progresses, the polymer gradually releases from the particles, allowing normal setting without hurting early strength. Interestingly, calcium ions present in the mix interact with the carboxylate groups on the polymer, subtly influencing the shape of the hydration crystals, potentially contributing to stronger concrete.
Polycarboxylate powders are also remarkably adaptable to tough site conditions. While dosage might need minor tweaks, they perform reliably across a wide range of temperatures, unlike many older admixtures. They also hold up well in high-salt environments (like coastal projects), resisting interference from ions that can disrupt other plasticizers. Even humidity, which affects how quickly the powder dissolves, is managed through specific formulation additives.
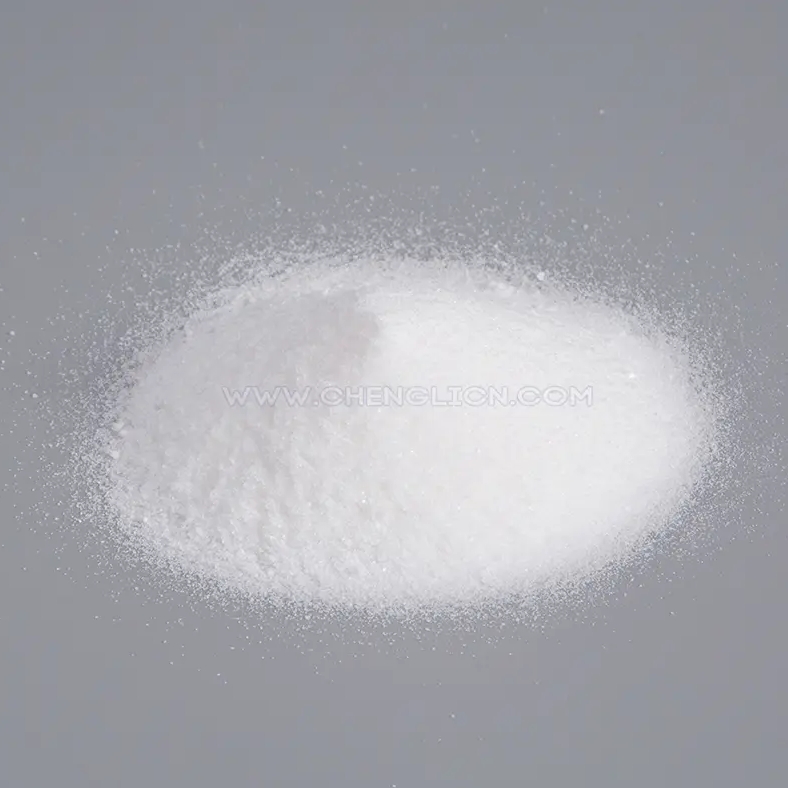
Producing such a consistent powder requires advanced techniques. Modern methods, like RAFT polymerization, allow precise control over the polymer’s chain lengths. Rigorous quality control ensures the final powder particles are uniformly sized, guaranteeing they dissolve evenly in the mix and deliver predictable results every time. Sustainable production methods are increasingly used, minimizing energy consumption and waste.
The proof is in real-world performance. This powder enables pumping concrete to incredible heights in skyscrapers, reducing friction in the pipes and saving energy. Precast concrete manufacturers get faster demolding times and flawlessly filled complex molds. Critical infrastructure like bridges and tunnels benefit from the enhanced long-term durability and reduced cracking under stress.
Looking ahead, research continues. Scientists are exploring biodegradable side chains to make these admixtures even more environmentally friendly. Integrating nanotechnology could further improve dispersion and boost early strength. Excitingly, machine learning is now being used to predict the optimal superplasticizer formulation for specific concrete recipes, pushing the boundaries of what’s possible.
Polycarboxylate superplasticizer powder is a true triumph of materials science. Its intelligent molecular design, effective action, and adaptability have fundamentally changed concrete technology. As construction demands grow ever more complex, the science behind this remarkable powder will continue to evolve.