Introduction: Why Concrete Needs Backup
Our buildings, bridges, and roads face a daily chemical onslaught. Think de-icing salts eating away at highways, factory acids splashing on floors, or seawater sulfates attacking piers. Ordinary concrete often loses this battle, cracking and crumbling prematurely. This means expensive fixes and shorter lifespans. Thankfully, a powerful ally exists: silica fume. Adding this unassuming powder gives concrete a remarkable boost in fighting off chemical damage.
So, What is This Silica Fume Stuff?
Picture the intense heat of making silicon metal or ferrosilicon alloys. That process creates an ultrafine dust – that’s silica fume. Workers capture it before it escapes into the air. This dust consists of incredibly tiny, round particles. They’re almost pure silicon dioxide (SiO₂), but in a non-crystalline, “amorphous” form. To grasp its size, imagine particles about 100 times smaller than a grain of cement. This extreme fineness is its superpower. You might hear it called microsilica. It usually looks like a very fine grey powder. Don’t underestimate it; this powder packs a serious punch for concrete performance.
The Science Bit: Plugging the Leaks
Silica fume transforms concrete from the inside out. Its microscopic particles act like super-fine sand, filling the tiny gaps between the much larger cement grains. We call this the “filler effect.” But the real magic happens chemically. When cement mixes with water, it forms calcium hydroxide (CH), a relatively weak compound. Silica fume reacts with this CH. This “pozzolanic reaction” creates more calcium silicate hydrate (C-S-H) – the super-strong glue that holds concrete together. The result? A concrete structure that’s incredibly dense and much harder for liquids or gases to pass through. Essentially, silica fume plugs the microscopic holes and reinforces the concrete’s skeleton, building a formidable barrier against invaders.
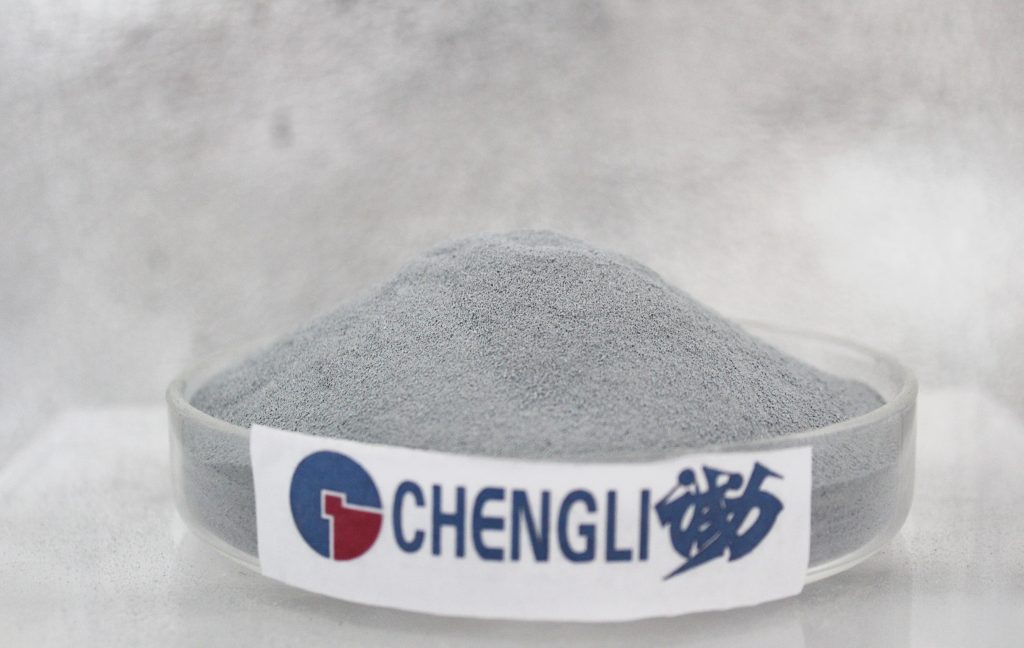
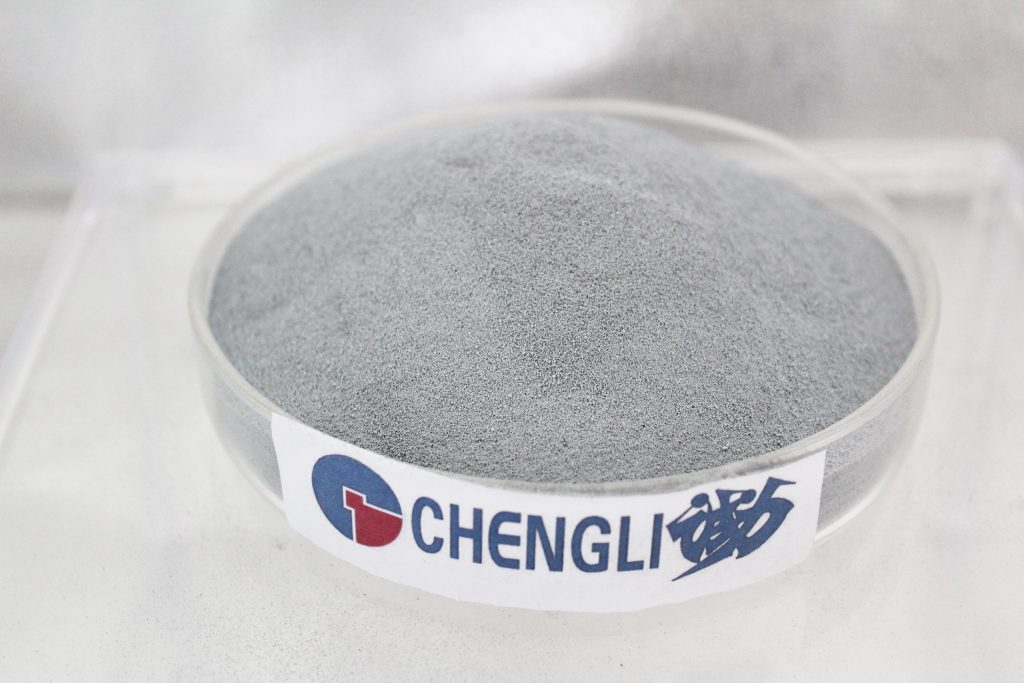
Why Density Wins the Chemical War
Making concrete denser is like putting up a stronger, taller fence. Aggressive chemicals – chloride ions from salt, sulfates, acids – find it much harder to penetrate deeply. They move slower and face greater resistance getting inside. This slow-down is crucial. For steel reinforcement bars buried inside concrete, it dramatically delays the start of rusting caused by chlorides. It also hinders destructive chemical reactions within the concrete paste itself. Less stuff gets in, less damage happens over the long haul.
Silica Fume’s Chemical Fighting Prowess
- Chloride Ion Invasion: Chlorides are public enemy number one for steel reinforcement, causing destructive rust. Silica fume concrete acts like a shield. Its low permeability drastically slows down how fast chlorides can seep in. This pushes back the “corrosion start clock,” a lifesaver for bridges, parking garages soaked in winter salt, and anything near the sea. Lab tests consistently prove its superior chloride resistance.
- Sulfate Siege: Sulfates lurking in soil or seawater can make concrete swell and crack. Silica fume’s dense matrix physically blocks sulfate ions. Plus, by consuming excess calcium hydroxide (the stuff sulfates love to attack), it leaves less vulnerable material behind. Structures in sulfate-heavy places get a vital durability upgrade.
- Acid Attacks: Concrete will always struggle against strong acids, but silica fume gives it better armor. Reduced permeability means acids can’t soak in as easily. Lower calcium hydroxide content also helps – there’s less soluble material for the acid to dissolve on the surface. Degradation happens much slower than in regular concrete.
- Alkali-Silica Reaction (ASR): This nasty reaction causes internal cracking. Silica fume helps fight it too. By refining the pore structure, it limits water movement needed for the damaging ASR gel to expand. It also soaks up some of the alkalis involved in the reaction, reducing their availability. It’s an important line of defense against this internal enemy.
Getting the Best Results: Mix and Cure Right
Just adding silica fume isn’t enough; you need to do it properly. We typically mix in 5-10% silica fume by weight of the cement. But here’s the catch: its fineness makes the concrete mix thirstier. You absolutely must use high-range water reducers (superplasticizers). These keep the concrete workable without adding extra water, which would weaken it. Thorough mixing is non-negotiable to spread those ultra-fine particles evenly. And curing? It’s even more critical than usual. Good, long moist curing lets the pozzolanic reaction finish its job, creating the densest, toughest structure possible. Skimp on curing, and you waste silica fume’s potential.
Bonus Benefits: More Than Just Chemistry
The perks don’t stop at chemical resistance. Silica fume significantly jacks up compressive strength – think 15,000 psi and beyond. It also improves flexural strength (bending resistance) and how well concrete grips onto steel reinforcement. Surfaces become much harder and more abrasion-resistant, perfect for busy factory floors or roads. It even reduces “bleeding” – that watery film that sometimes forms on top – leading to better surface quality and easier finishing.
Where This Super-Concrete Shines
Engineers choose silica fume concrete when chemical durability is critical:
- Ocean Frontlines: Piers, seawalls, harbors, offshore oil rigs – constantly battling seawater salts and sulfates.
- Bridges & Highways: Shielding structures from relentless de-icing salts and pollution.
- Chemical Zones: Factory floors, containment areas needing resistance to spills, acids, and heavy wear.
- Wastewater Worlds: Treatment plants exposed to corrosive hydrogen sulfide and microbes.
- Parking Fortresses: Multi-story garages protecting against salt dripping from cars all winter.
- Farm Tough: Barns and processing plants resisting acids from animal waste and fertilizers.
Silica Fume Concrete vs. The Regular Stuff: The Key Differences
Forget complex tables. Think of silica fume concrete as the upgraded model. Its standout features are much lower permeability (things can’t seep through easily), excellent chloride resistance (rust takes much longer to start), and significantly better sulfate resistance. While still vulnerable to strong acids, it holds up better than regular concrete. Strength gets a massive boost – it’s much harder to crush. Surfaces also become far more resistant to scraping and wear. Regular concrete simply can’t match this level of toughness against chemicals and physical stress.
Facing the Realities: Challenges and Cost
Let’s be honest, silica fume isn’t magic fairy dust. Handling the ultrafine powder requires care to avoid dust clouds; using pre-densified forms or slurries helps. The material itself costs more than plain cement. Precision in mix design and strict quality control on-site are essential. Contractors need to adjust techniques because the mix is stickier. However, the payoff comes later. Structures last decades longer and need far fewer repairs. This usually means a much better return on investment over the structure’s entire life. You pay more upfront for less hassle and cost down the road.
Conclusion: Building Tough for the Long Haul
Silica fume has revolutionized how we make concrete durable. Its power lies in creating an incredibly dense, nearly impermeable structure that stands firm against chemical aggression. Whether it’s the constant salt barrage on a bridge, sulfates in the ground, or occasional acid spills, silica fume concrete offers superior resilience. Yes, it demands careful use, but the reward is infrastructure built to last generations, requiring minimal repairs. Choosing silica fume means building with the future in mind – creating safer, longer-lasting, and truly sustainable structures ready to face the harsh chemical realities of our world. It transforms concrete from a temporary fix into a genuinely enduring solution.
Our Professional Technical Team Is Available 24/7 To Address Any Issues You May Encounter While Using Our Products. We Look Forward To Your Cooperation!