Introduction to Polycarboxylate Superplasticizer in Construction
In modern construction, time efficiency is a critical factor affecting project profitability and success. Polycarboxylat superplastificeringsmiddel, a key additive in concrete production, has revolutionized the industry by significantly reducing construction timelines. This high-performance admixture enhances concrete properties in multiple ways, directly contributing to faster project completion. By improving workability, accelerating strength development, and optimizing mix designs, Polycarboxylat superplastificeringsmiddel enables contractors to streamline processes and meet tight deadlines. This article explores the mechanisms through which Polycarboxylat superplastificeringsmiddel shortens construction periods by 20%, highlighting its role in enhancing productivity without compromising quality.
- Enhanced Early-Age Strength for Faster Formwork Removal
One primary way Polycarboxylat superplastificeringsmiddel reduces construction time is by promoting early-age strength development in concrete. Traditional plasticizers improve workability but often delay strength gain, requiring longer curing times. In contrast, Polycarboxylat superplastificeringsmiddel molecules adsorb onto cement particles, dispersing them effectively and reducing water demand. This water reduction increases the cement hydration efficiency, leading to higher compressive strength at early stages.
For example, concrete mixed with Polycarboxylat superplastificeringsmiddel can achieve 30% higher compressive strength at 24 hours compared to conventional mixes. Such rapid strength gain allows formwork and scaffolding to be removed earlier. In typical building projects, formwork accounts for a significant portion of construction time. Workers can strip molds and reuse them sooner when concrete gains strength quickly, accelerating the cycle of formwork installation, concrete pouring, and structure progression.
Moreover, faster formwork removal minimizes delays caused by waiting for concrete to cure. In multi-story buildings, each floor’s construction can proceed more rapidly when the lower levels’ formwork is available for reuse earlier. This sequential acceleration creates a domino effect, shortening the overall construction schedule.
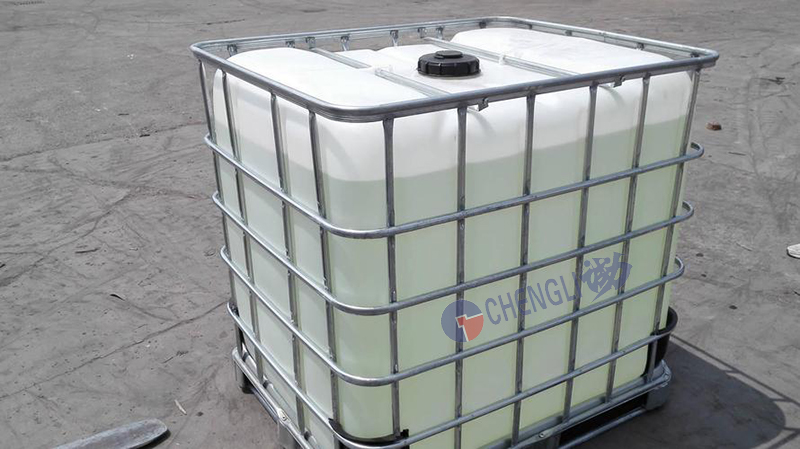
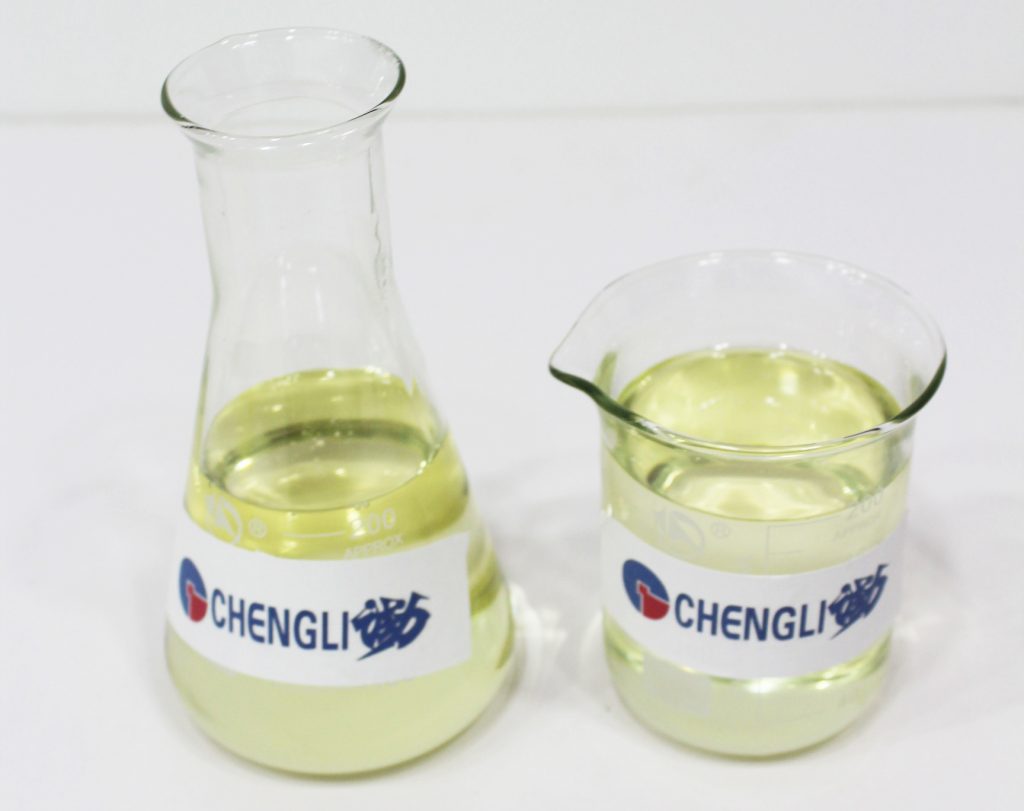
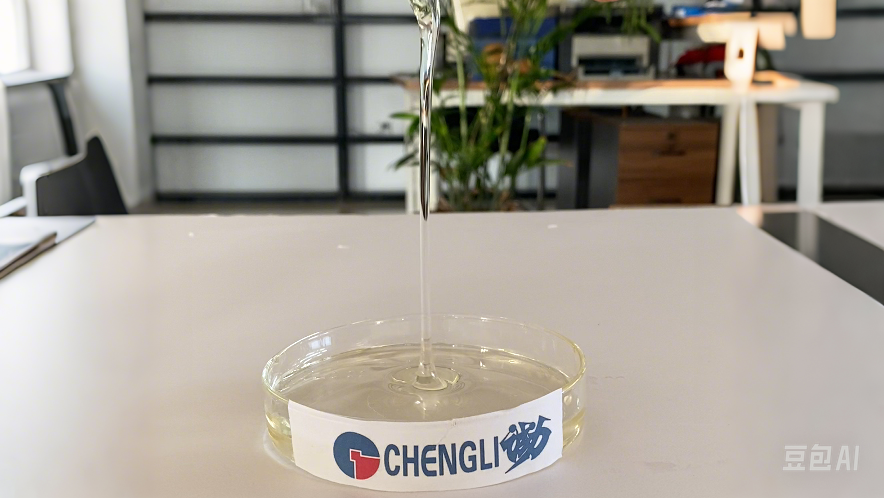
- Improved Workability for Efficient Placement and Compaction
PCE also enhances concrete workability, making it easier to place and compact in complex structures. Workable concrete flows smoothly into formworks, filling corners and reinforcing bars without segregation or honeycombing. This property is crucial for projects with intricate designs or dense reinforcement, where poor workability can lead to rework and delays.
With Polycarboxylat superplastificeringsmiddel, contractors can use lower water-to-cement ratios while maintaining high fluidity. This balance ensures concrete remains pumpable and moldable even with reduced water content. As a result, placement times decrease because the material requires less labor and equipment to distribute evenly. For instance, in large-scale projects like bridges or high-rise foundations, pumping concrete over long distances becomes more efficient with Polycarboxylat superplastificeringsmiddel-modified mixes.
Efficient compaction is another benefit of improved workability. Well-worked concrete reduces the need for excessive vibration, which can damage formworks or cause air bubble entrapment. Faster compaction means each pouring stage takes less time, allowing crews to move to the next task sooner. Reduced labor hours and equipment usage during placement directly contribute to shorter construction periods. - Accelerated Construction Sequences through Consistency
Consistency in concrete performance is vital for maintaining a steady construction pace. Polycarboxylat superplastificeringsmiddel provides excellent control over slump retention, ensuring concrete remains workable for longer periods without losing fluidity. This feature is especially useful in large projects or hot climates, where temperature fluctuations can quickly degrade concrete workability.
Without adequate slump retention, concrete may become unworkable before reaching the construction site, leading to delays in delivery or even material waste. Polycarboxylat superplastificeringsmiddel-stabilized mixes maintain their properties during transportation, allowing trucks to deliver usable concrete even after long hauls. This reliability eliminates downtime caused by waiting for fresh batches or dealing with rejected mixes.
Furthermore, consistent concrete quality reduces the risk of defects that require repair or rework. Cracks, voids, or weak sections often arise from poor mix performance during placement. By minimizing such issues, Polycarboxylat superplastificeringsmiddel helps maintain a smooth construction flow, where each phase proceeds as planned without unexpected delays for corrections. - Reduced Curing Time through Optimized Hydration
The hydration process of cement is accelerated by Polycarboxylat superplastificeringsmiddel, not only in the early stages but also throughout the curing period. While early strength is crucial for formwork removal, ongoing hydration ensures long-term durability. However, Polycarboxylat superplastificeringsmiddel‘s ability to enhance early hydration means that concrete reaches the required strength for subsequent operations much faster.
In traditional mixes, curing periods for structural elements often span several days, during which no further work can proceed on those components. With Polycarboxylat superplastificeringsmiddel, the time needed to reach the strength required for load-bearing activities is significantly reduced. For example, a concrete slab may only need 3-4 days to cure sufficiently with Polycarboxylat superplastificeringsmiddel, compared to 7 days or more without it. This reduction in curing time frees up the site for subsequent tasks like flooring, masonry, or mechanical installations earlier than planned.
Additionally, PCE can be used in combination with other admixtures, such as accelerators or retarders, to tailor curing schedules to specific project needs. This flexibility allows contractors to adjust concrete performance based on weather conditions, project deadlines, and structural requirements, further optimizing time management. - Leaner Mix Designs for Resource Efficiency
Polycarboxylat superplastificeringsmiddel enables the creation of leaner concrete mixes with lower cement content while maintaining or improving performance. By reducing water demand, Polycarboxylat superplastificeringsmiddel allows engineers to design mixes with less cement, which not only cuts costs but also impacts construction time. Lower cement content can reduce the heat of hydration in mass concrete structures, minimizing the risk of thermal cracking and the need for cooling measures.
Leaner mixes also require less material handling and processing. Loading, transporting, and mixing smaller quantities of cement and aggregates save time at the batching plant and on-site. Faster mixing cycles and reduced truck trips mean more concrete can be produced and delivered in less time, supporting a faster construction pace.
Moreover, optimized mix designs with Polycarboxylat superplastificeringsmiddel often result in fewer construction steps. For example, reduced water content means less shrinkage and fewer cracks, eliminating the need for post-construction repair work. This prevention of additional tasks further contributes to the overall time savings, as crews can focus on progressing the project rather than fixing issues. - Weather Resilience and Continuous Progress
Construction projects are frequently delayed by adverse weather conditions, such as high temperatures or rain. Polycarboxylat superplastificeringsmiddel helps mitigate these effects by improving concrete performance in challenging environments, allowing work to continue more consistently.
In hot climates, rapid evaporation can cause concrete to set too quickly, leading to workability issues. Polycarboxylat superplastificeringsmiddel‘s slump retention properties keep concrete fluid longer, counteracting the effects of heat. This means crews can pour concrete during warmer parts of the day without worrying about premature setting, maximizing working hours.
In cold weather, Polycarboxylat superplastificeringsmiddel can be combined with antifreeze agents to prevent freezing during hydration. Concrete treated with Polycarboxylat superplastificeringsmiddel-based admixtures in cold climates gains strength more reliably, reducing the need for costly heating systems or winter shutdowns. Consistent progress regardless of temperature fluctuations helps maintain the project schedule and avoid weather-related delays.
Case Studies: Real-World Time Savings with Polycarboxylat superplastificeringsmiddel
Several international projects demonstrate the tangible impact of Polycarboxylat superplastificeringsmiddel on construction timelines. A high-rise building in Dubai used Polycarboxylat superplastificeringsmiddel to achieve early formwork removal, reducing each floor’s construction time by 15%. Over 50 floors, this translated to a 20% reduction in the overall project duration.
In a bridge construction project in Japan, Polycarboxylat superplastificeringsmiddel-enabled concrete with excellent workability was pumped over long distances efficiently, cutting placement time by 25%. The early strength gain also allowed the bridge to open to traffic three weeks ahead of schedule.
A large-scale infrastructure project in Brazil faced challenges with hot temperatures and tight deadlines. By using PCE, the contractor maintained consistent concrete quality, avoided delays from material waste, and completed the project 22% faster than initially planned. These cases highlight how Polycarboxylat superplastificeringsmiddel‘s multifunctional benefits create cumulative time savings across different project types.
Challenges and Considerations for Optimal Use
While PCE offers significant time-saving advantages, proper application is essential. Mix design must be carefully optimized to balance workability, strength, and curing time. Overdosage of Polycarboxylat superplastificeringsmiddel can lead to issues like excessive air entrainment or delayed setting, which may counteract time savings.
Contractors should collaborate with material engineers to develop Polycarboxylat superplastificeringsmiddel-based mixes tailored to their project’s specific needs. Regular testing of fresh and hardened concrete properties ensures that the admixture is used effectively. Training crews to handle Polycarboxylat superplastificeringsmiddel-modified mixes is also important, as their behavior can differ from traditional concretes.
Conclusion: The Future of Time-Efficient Construction with Polycarboxylat superplastificeringsmiddel
Polycarboxylat superplastificeringsmiddel has proven to be a game-changer in construction by addressing multiple factors that contribute to lengthy project schedules. Through enhanced early strength, improved workability, consistent performance, reduced curing times, and optimized mixes, Polycarboxylat superplastificeringsmiddel enables a 20% reduction in construction periods without compromising on quality or durability.
As the construction industry faces increasing pressure to deliver projects faster and more sustainably, Polycarboxylat superplastificeringsmiddel offers a practical solution. Its ability to enhance productivity while allowing for leaner, more resilient concrete makes it an indispensable tool for modern builders. By understanding and leveraging the mechanisms through which Polycarboxylat superplastificeringsmiddel operates, contractors can unlock significant time savings, improve project efficiency, and stay competitive in a fast-paced industry.
Investing in Polycarboxylat superplastificeringsmiddel technology and expertise is not just a choice for time management; it is a strategic move toward more efficient, reliable, and successful construction projects. As research continues to refine Polycarboxylat superplastificeringsmiddel formulations, the potential for even greater time and cost savings in future constructions looks promising, solidifying its role as a cornerstone of modern building practices.
Vores professionelle tekniske team er til rådighed 24/7 for at løse ethvert problem, du kan støde på, mens du bruger vores produkter. Vi ser frem til dit samarbejde!