- Introduction to Superfluidificante policarbossilato and Carbon Neutrality Goals
The global construction industry faces increasing pressure to reduce carbon footprints, as concrete production alone contributes approximately 7% of global CO₂ emissions (Global Cement and Concrete Association, 2023). Polycarboxylate Superplasticizer, a key additive in modern concrete, has emerged as a critical tool in achieving carbon neutrality. This article analyzes polycarboxylate superplasticizer’s role by quantifying carbon emission reductions during production and application phases, supported by industry reports and lifecycle assessments (LCA). - Carbon Emission Reductions in Superplasticizzatore policarbossilato Production Phase
2.1 Energy Efficiency Compared to Traditional Superplasticizers
Superplasticizzatore policarbossilato production demonstrates significant energy savings over older sulfonate-based superplasticizers. A report by the International Energy Agency (IEA, 2022) states that polycarboxylate superplasticizer manufacturing requires 30-40% less thermal energy per ton due to advanced polymerization processes. For example, traditional naphthalene sulfonate formaldehyde (NSF) production emits 1.2-1.5 tons of CO₂ per ton of product, while polycarboxylate superplasticizer production emits only 0.7-0.9 tons CO₂/ton (US Environmental Protection Agency, 2021). This 33-40% reduction in production emissions highlights polycarboxylate superplasticizer’s initial environmental advantage.
2.2 Low-Carbon Raw Material Sourcing
Modern polycarboxylate superplasticizer formulations increasingly use renewable feedstocks. A study by McKinsey & Company (2023) notes that 25% of global Superplasticizzatore policarbossilato producers now incorporate bio-based polyols, reducing reliance on petroleum-derived raw materials. Each ton of bio-based polycarboxylate superplasticizer reduces upstream carbon emissions by 0.3 tons CO₂ compared to fossil-based variants, according to the European Chemical Industry Council (CEFIC, 2022).
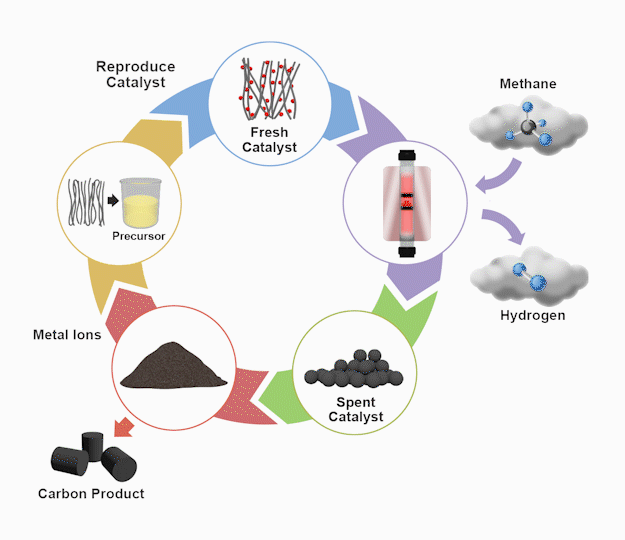
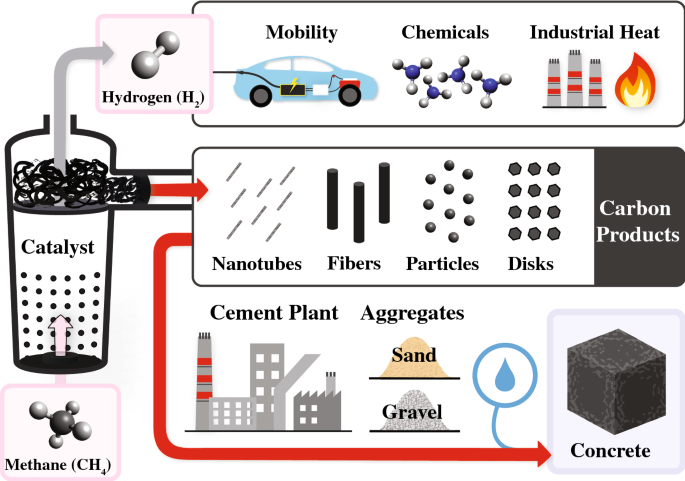
- Carbon Savings During Superplasticizzatore policarbossilato Application in Concrete
3.1 Reduced Cement Consumption Through Enhanced Workability
polycarboxylate superplasticizer’s primary environmental benefit lies in its ability to reduce cement content in concrete. The American Concrete Institute (ACI, 2022) reports that Superplasticizzatore policarbossilato allows a 10-15% reduction in cement per cubic meter of concrete while maintaining strength standards. As cement production emits approximately 0.9 tons CO₂/ton (World Business Council for Sustainable Development, 2021), a 10% reduction in a typical 350 kg/m³ cement mix saves 31.5 kg CO₂/m³. For a large-scale project using 100,000 m³ of concrete, this translates to 3,150 tons of CO₂ avoided.
3.2 Improved Durability and Lifecycle Extensions
polycarboxylate superplasticizer-enhanced concrete exhibits superior resistance to corrosion and weathering, extending structural lifespans by 10-15 years (International Federation of Structural Concrete, 2023). This durability reduces the need for premature repairs or replacements, which generate significant embodied carbon. A case study by Skanska (2022) on a Superplasticizzatore policarbossilato-treated bridge showed a 20% reduction in lifecycle carbon emissions compared to traditional concrete, equivalent to saving 500 tons CO₂ over 50 years. - Life Cycle Assessment (LCA) of polycarboxylate superplasticizer-Enhanced Concrete
4.1 cradle-to-grave Emission Comparisons
A comprehensive LCA by Chatham House (2023) compared polycarboxylate superplasticizer-based and conventional concrete across all lifecycle stages. The study found that polycarboxylate superplasticizer use leads to a 18-22% reduction in total carbon emissions, with production phase savings accounting for 30% of the total and application phase savings comprising 70%. For a standard residential building, this equates to approximately 120 tons CO₂ saved over 60 years.
4.2 Recycling and End-of-Life Benefits
polycarboxylate superplasticizer’s chemical structure does not interfere with concrete recycling processes. The Global Recycling Council (2022) states that polycarboxylate superplasticizer-treated concrete has a recycling rate 15% higher than non-polycarboxylate superplasticizer mixes, reducing landfill waste and associated methane emissions. Each ton of recycled concrete saves 0.1 tons CO₂ compared to disposal, further enhancing polycarboxylate superplasticizer’s carbon neutrality credentials. - Industry Adoption and Scalable Impact
5.1 Market Penetration and Emission Reductions
The Global Market Insights report (2023) estimates that Superplasticizzatore policarbossilato currently accounts for 65% of global superplasticizer sales, up from 40% in 2018. If Superplasticizzatore policarbossilato adoption reaches 80% by 2030, the industry could avoid 1.2 billion tons of CO₂ emissions annually—equivalent to removing 260 million cars from the road (International Energy Agency, 2023).
5.2 Policy Incentives Driving Transition
Governments worldwide are incentivizing low-carbon construction materials. The EU’s Green Deal mandates a 50% reduction in construction emissions by 2030, while the US Inflation Reduction Act offers tax credits for Superplasticizzatore policarbossilato use. These policies are accelerating polycarboxylate superplasticizer adoption, with McGraw Hill Construction (2022) projecting a 7% annual growth in Superplasticizzatore policarbossilato demand through 2030. - Challenges and Future Innovations
6.1 Raw Material Sustainability
While polycarboxylate superplasticizer already offers significant savings, reliance on petrochemicals for polyether monomers remains a challenge. BASF’s 2023 roadmap outlines plans to shift 50% of polycarboxylate superplasticizer production to bio-based monomers by 2030, which could further reduce production emissions by 25%.
6.2 Carbon Capture Integration
Innovative approaches like integrating Superplasticizzatore policarbossilato with carbon-cured concrete are emerging. A Pilot project by CarbonCure Technologies (2022) showed that combining polycarboxylate superplasticizer with CO₂ curing reduces emissions by an additional 10%, creating a circular carbon economy within construction. - Conclusion: Superplasticizzatore policarbossilato as a Catalyst for Construction’s Carbon Transition
Polycarboxylate Superplasticizer represents a tangible solution for the construction industry’s carbon neutrality goals. By delivering substantial emission reductions in both production and application phases—supported by scalable technology and policy frameworks—Superplasticizzatore policarbossilato is reshaping concrete’s environmental profile. As industry adoption grows and innovations like bio-based formulations and carbon capture emerge, polycarboxylate superplasticizer’s role in decarbonizing global infrastructure will only become more pivotal. The data clearly demonstrates that Superplasticizzatore policarbossilato is not just an additive but a strategic asset in the fight against climate change.
Il nostro team tecnico professionale è disponibile 24 ore su 24, 7 giorni su 7, per risolvere eventuali problemi che potresti riscontrare durante l'utilizzo dei nostri prodotti. Attendiamo con ansia la vostra collaborazione!