Beating Concrete’s Summer Enemy
Pouring concrete under a blazing sun comes with big challenges. Accelerated setting times turn into a major headache. Fast hydration saps away crucial workability, forcing crews to rush placements and scramble through finishing. This hurry often hurts the final structure’s strength and surface quality. When the heat cranks up, using a reliable retarding agent isn’t just helpful—it’s essential. And time and again, sodium gluconate proves itself as the top choice for consistent, predictable concrete retardation in those tough hot-weather conditions.
Sodium Gluconate: The Heat-Fighting Workhorse
Builders swear by sodium gluconate for its standout performance. This white, crystalline powder dissolves easily in water, and its organic makeup and unique molecular structure give it serious retarding power. It’s made by fermenting glucose—usually from corn—and works its magic without harming the environment or construction crews. Plus, it’s non-corrosive, making handling safe and straightforward.
Slowing Hydration: How It Gets the Job Done
So how exactly does sodium gluconate tackle the heat? The secret lies in how it interacts with cement particles. As soon as the mix is blended, the compound clings to the surface of cement grains. Sodium gluconate molecules act like a shield, covering the reactive spots on those grains. This protective layer slows down the early hydration reactions that matter most. Water can’t reach the cement minerals as easily, so the formation of the rigid compounds that cause setting takes much longer. This controlled delay gives crews the extra workability time they desperately need during summer pours. And with the right dosage, the retarding effect stays predictable and easy to manage.
Key Benefits When the Temperature Spikes
Gluconato di sodio delivers real advantages for concrete producers and contractors when it’s sweltering outside:
- More Time to Place and Finish: Crews get vital extra minutes—even hours. This flexibility lets them properly consolidate the mix, add detailed finishes, and handle unexpected delays without rushing. Getting a smooth, professional finish becomes much easier.
- Better Workability Retention: Concrete stays plastic and flowable longer, so slump loss is minimized. Pumping and placing the mix stays efficient from start to finish, and workers don’t strain as much moving stiffening concrete.
- Stronger Long-Term Strength: Controlled hydration leads to better curing over time. The hardened concrete develops a more uniform structure, which often means higher compressive and flexural strengths in the end. It also holds up better against the elements.
- Fewer Cold Joints: Slower setting drastically cuts down on weak spots forming between successive pours. This keeps the structure continuous and solid—critical for large slabs, walls, and key structural parts.
- Improved Surfaces: By preventing quick moisture loss and premature stiffening, sodium gluconate reduces surface flaws. It’s easier to avoid plastic shrinkage cracks and dusting, so finishers can get smoother, denser, and better-looking surfaces.
- Cost-Effective Results: A little goes a long way with sodium gluconate. It works efficiently at low dosages, optimizing mix designs and cutting down on rework. The savings from better performance often outweigh the cost of the additive itself.
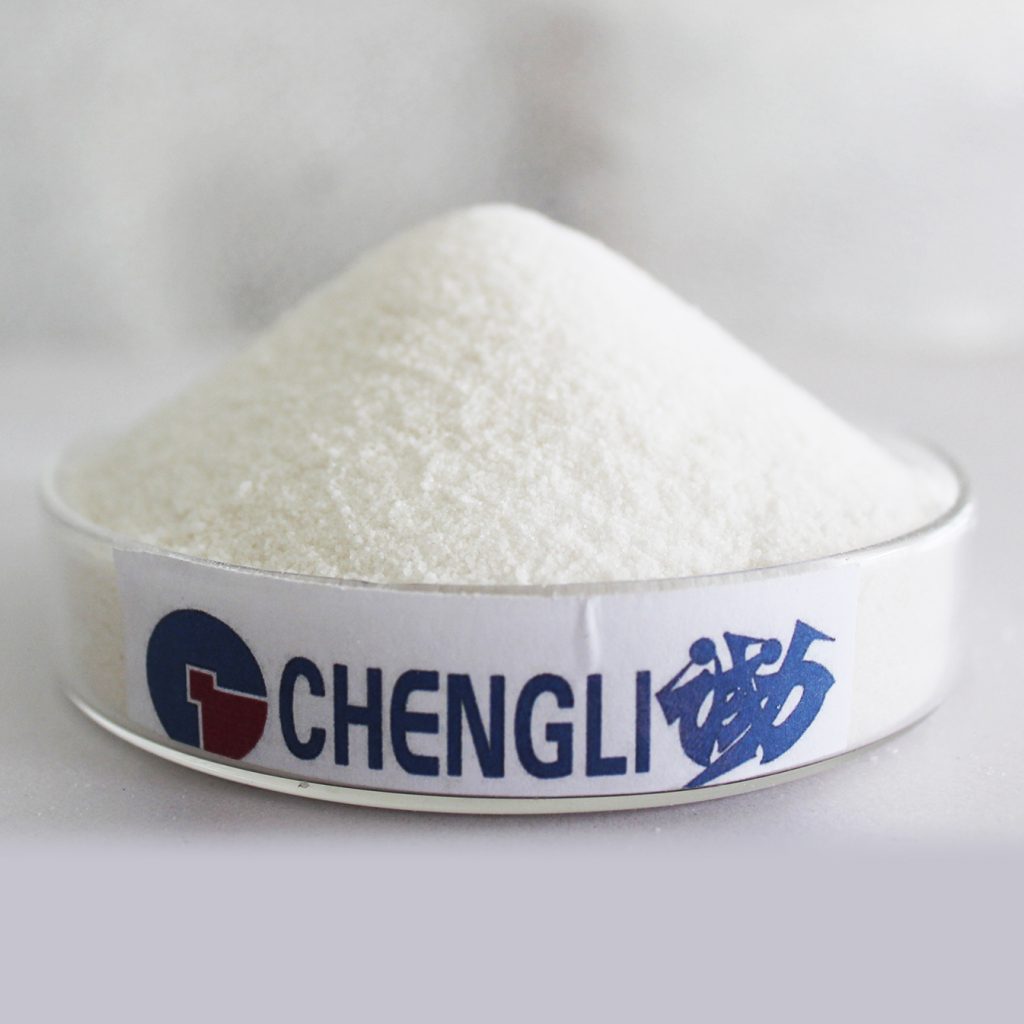
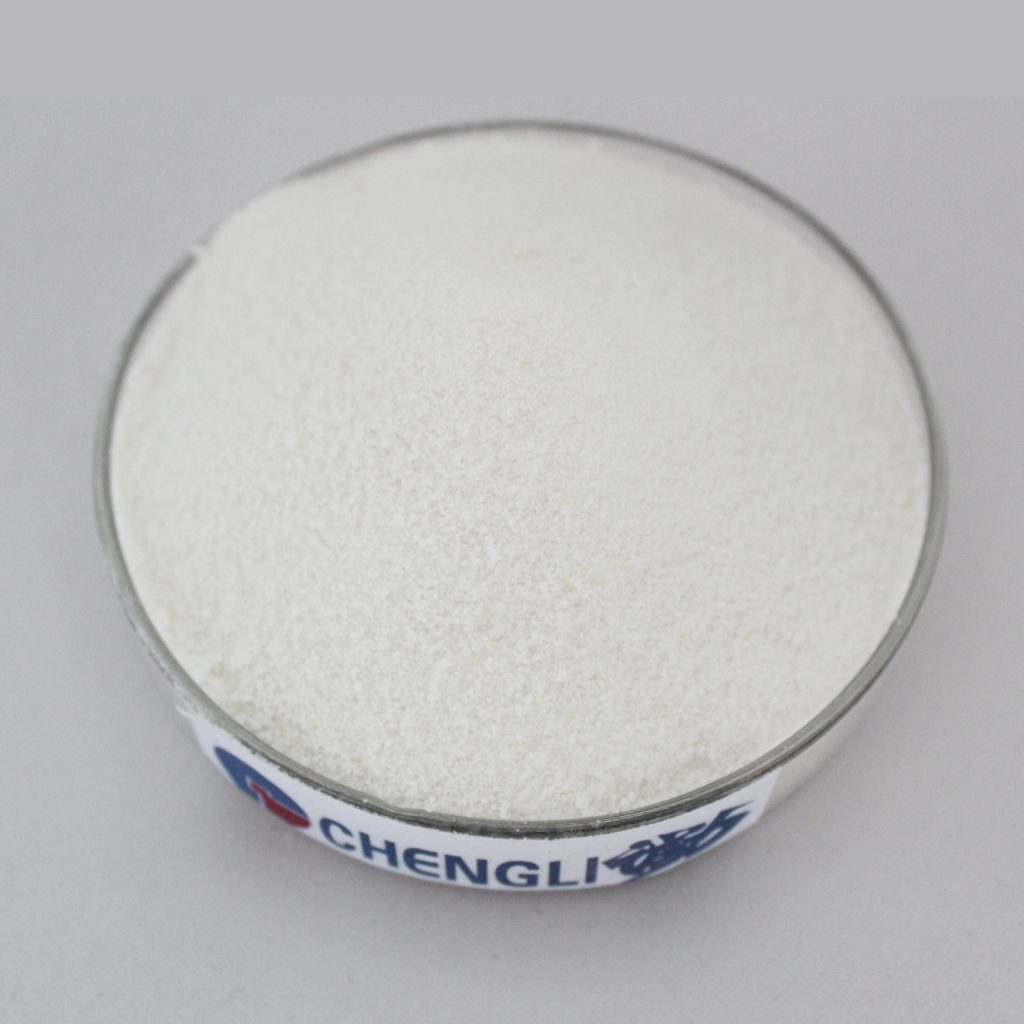
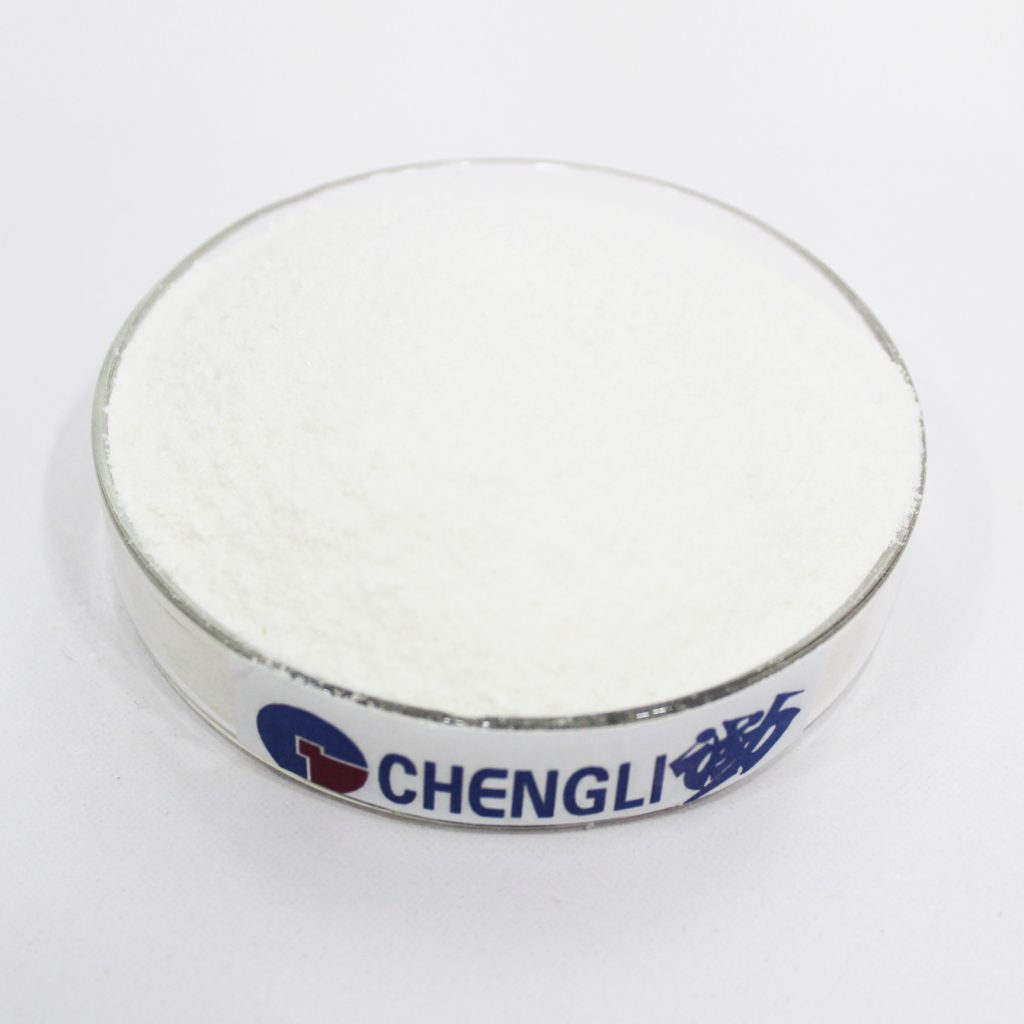
Real-World Example: A Summer Bridge Project
Take a major bridge deck pour scheduled during a July heatwave, for instance. Ambient temps hit over 95°F (35°C), and direct sunlight pushed surface temperatures even higher. Without a good retarder, the concrete might have become unworkable in just 20–30 minutes, leaving finishers struggling. But adding sodium gluconate at 0.08% by cement weight extended workability to 90 minutes. Crews placed and finished the deck calmly and thoroughly, and the result? A smooth surface with zero cold joints that passed tough inspections. Project managers avoided costly delays and fixes.
Using Sodium Gluconate Right: Pro Tips
To get the most out of sodium gluconate, pay attention to these details:
- Dosage Matters Most: The right amount depends on factors like cement type, ambient temperature, how long you need retardation, and other admixtures in the mix. Typical doses range from 0.05% to 0.15% by weight of cementitious materials. Always check supplier recommendations and run site-specific tests—never guess.
- Mix It Well: Get sodium gluconate evenly distributed. Adding it directly to the mixer with the batch water works, but pre-dissolving it in a small amount of mixing water is often better. Make sure it’s fully dissolved before adding aggregates to avoid clumps and keep results consistent.
- Check Compatibility: Gluconato di sodio usually plays nice with other common admixtures like water reducers and air-entrainers, but double-check first—especially with high-range water reducers (superplasticizers). Lab tests upfront prevent messy interactions on-site, so always test the full mix of admixtures.
- Watch the Thermometer: As temperatures rise, you’ll need more sodium gluconate. Higher heat speeds up hydration, so a slight boost in dosage helps compensate. Keep an eye on weather forecasts before batching and adjust plans ahead of time.
- Don’t Overdo It: While effective, too much sodium gluconate can cause extreme retardation. Setting might get delayed way beyond what’s practical, and in bad cases, it could slow early strength development. Stick to recommended dosage ranges and follow supplier guidelines closely.
Why Sodium Gluconate Beats the Alternatives
There are other concrete retarders out there, but sodium gluconate often comes out on top:
- Compared to Lignosulfonates: Gluconato di sodio packs more retardation power per unit weight. It doesn’t reduce water or entrain air as much, letting you control the mix independently. Lignosulfonates can sometimes bring unpredictable results.
- Compared to Sugar: Sugar works but is unreliable—its performance changes with source and purity. Using too much can cause wild delays and weaken strength. Sodium gluconate offers consistent, controlled retardation.
- Compared to Hydroxycarboxylic Acids (like Citric Acid): Gluconato di sodio plays nicer with different cement types. It’s less likely to hurt early strength development and delivers more predictable results.
- Compared to Phosphates: Sodium gluconate is usually more affordable and easier to find. Phosphate-based retarders can sometimes mess with mix water chemistry, creating extra hassle.
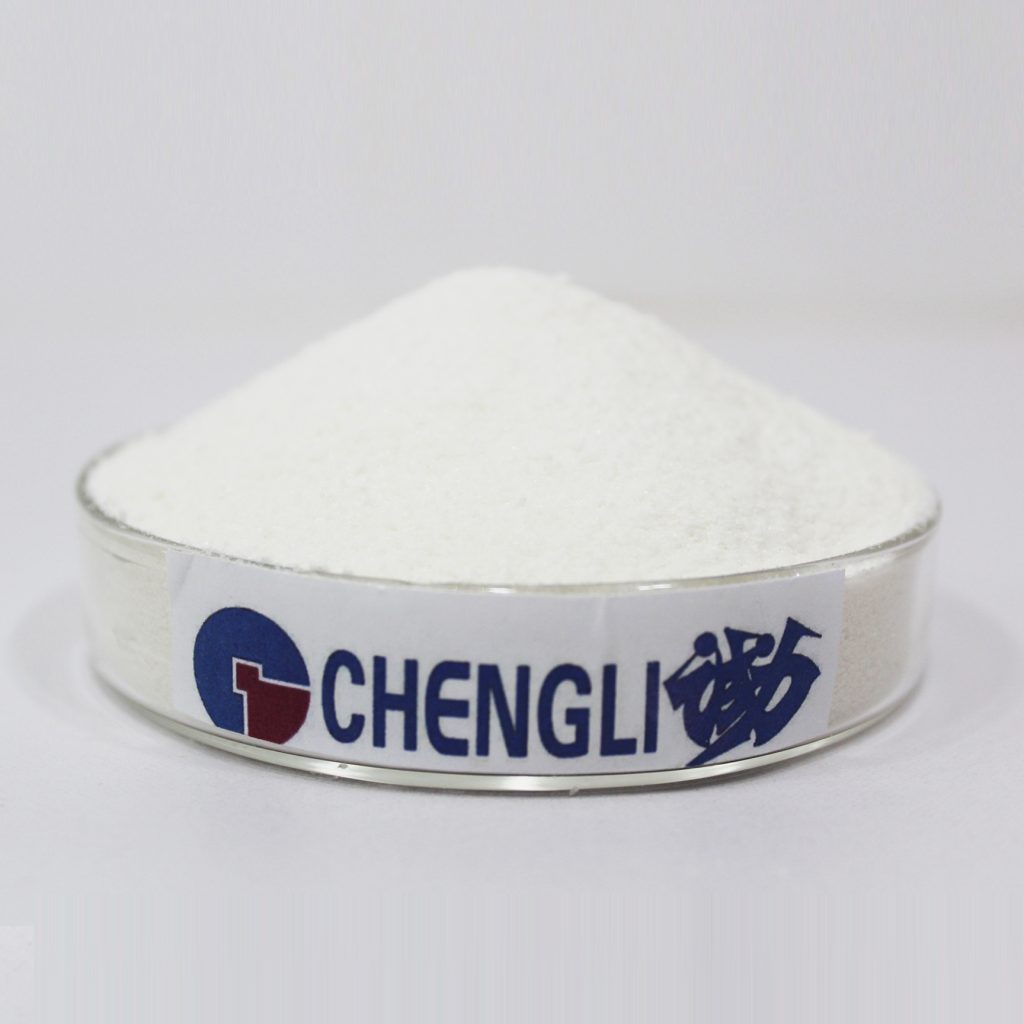
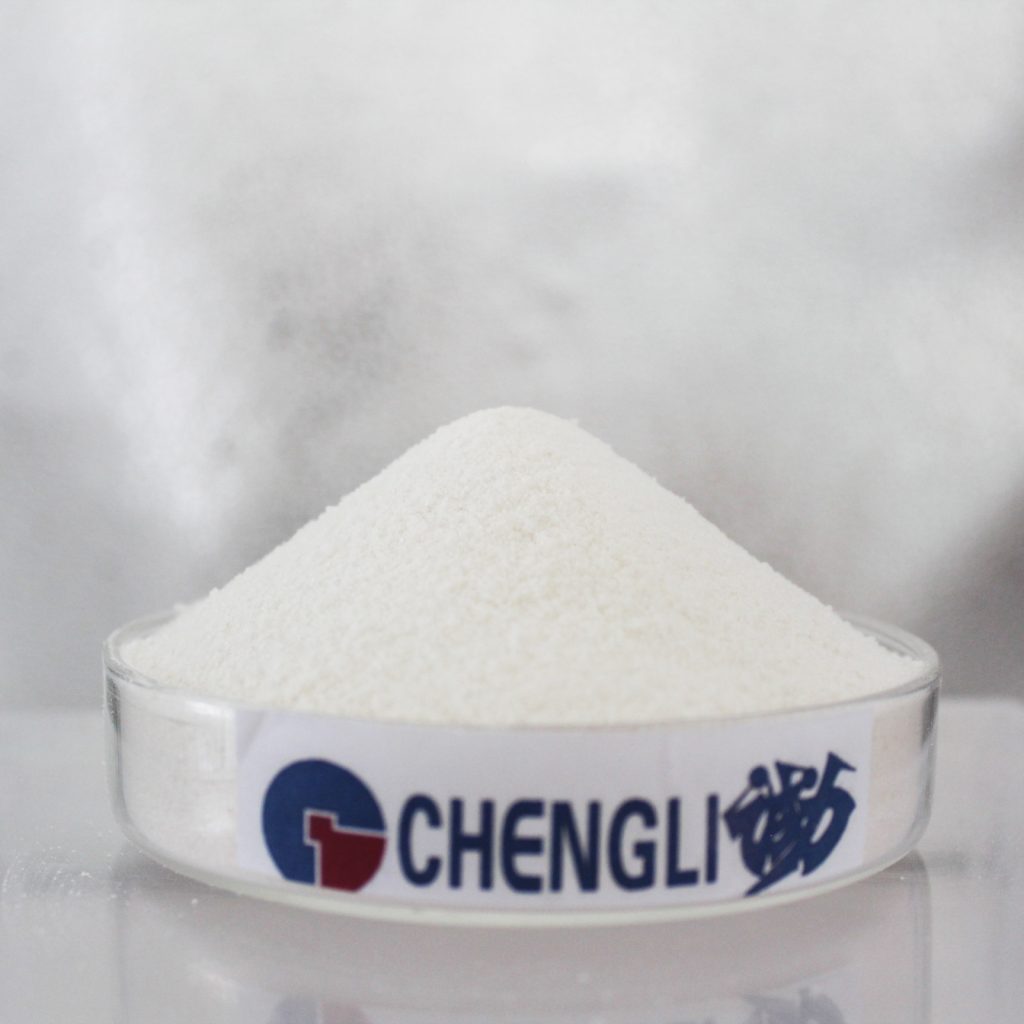
Mastering Hot-Weather Concreting: A Full Plan
Gluconato di sodio is a must, but successful hot-weather concreting needs a full strategy:
- Cool the Mix: Use chilled mixing water, swap some water for ice, or shade aggregate piles. For extreme heat, even liquid nitrogen injection can help. Lowering the initial concrete temperature is key.
- Protect the Placement: Set up sunshades and windbreaks right away. Direct sun and wind dry out surfaces fast, so keep that protection up until finishing is done.
- Moisten Subgrades and Forms: Dampen contact surfaces before pouring. Dry substrates suck moisture out of the concrete from the bottom—don’t let that happen.
- Plan Logistics: Organize delivery, placement, and finishing crews carefully. Minimize truck wait times and make sure all equipment works before starting—delays get costly in the heat.
- Start Curing Immediately: As soon as finishing wraps up, apply curing compounds or wet coverings. Stopping rapid moisture loss is critical for strength and durability—never let the surface dry out too soon.
Final Thought: The Smart Choice for Reliable Results
Hot weather puts concrete quality and construction efficiency to the test. In these tough conditions, sodium gluconate stands out as the most reliable, effective retarding agent. Its ability to consistently extend workability, improve finishes, and boost long-term strength makes it invaluable. By understanding how it works, nailing dosage and mixing best practices, and folding it into a full hot-weather plan, contractors can pull off successful pours even under the harshest summer sun. Choosing sodium gluconate means choosing control, quality, and confidence when the mercury rises—make it your go-to partner for summer concreting success.
Il nostro team tecnico professionale è disponibile 24 ore su 24, 7 giorni su 7, per risolvere eventuali problemi che potresti riscontrare durante l'utilizzo dei nostri prodotti. Attendiamo con ansia la vostra collaborazione!