In construction, concrete’s setting time isn’t just a detail—it’s the difference between a flawless pour and a costly failure. Pour too fast, and crews can’t properly place or finish it. Too slow, and projects stall. This precision balancing act is where sodium gluconate shines. Unlike generic additives, this organic compound gives engineers surgical control over concrete’s timeline, making it indispensable for modern builds from skyscrapers to sidewalks.
How It Works: The Science of Slowing Down
Sodium gluconate targets concrete’s hydration process—the chemical reaction that turns liquid mix into solid stone. When water hits cement, crystals form and rapidly interlock, hardening the mass. Sodium gluconate disrupts this dance in two smart ways:
- Ion Lockdown: It binds to calcium ions essential for crystal growth, delaying their assembly without stopping the reaction entirely.
- Surface Shield: The compound coats cement particles, creating a barrier that slows water penetration and reaction speed.
The result? A predictable, adjustable working window that holds across cement types and conditions.
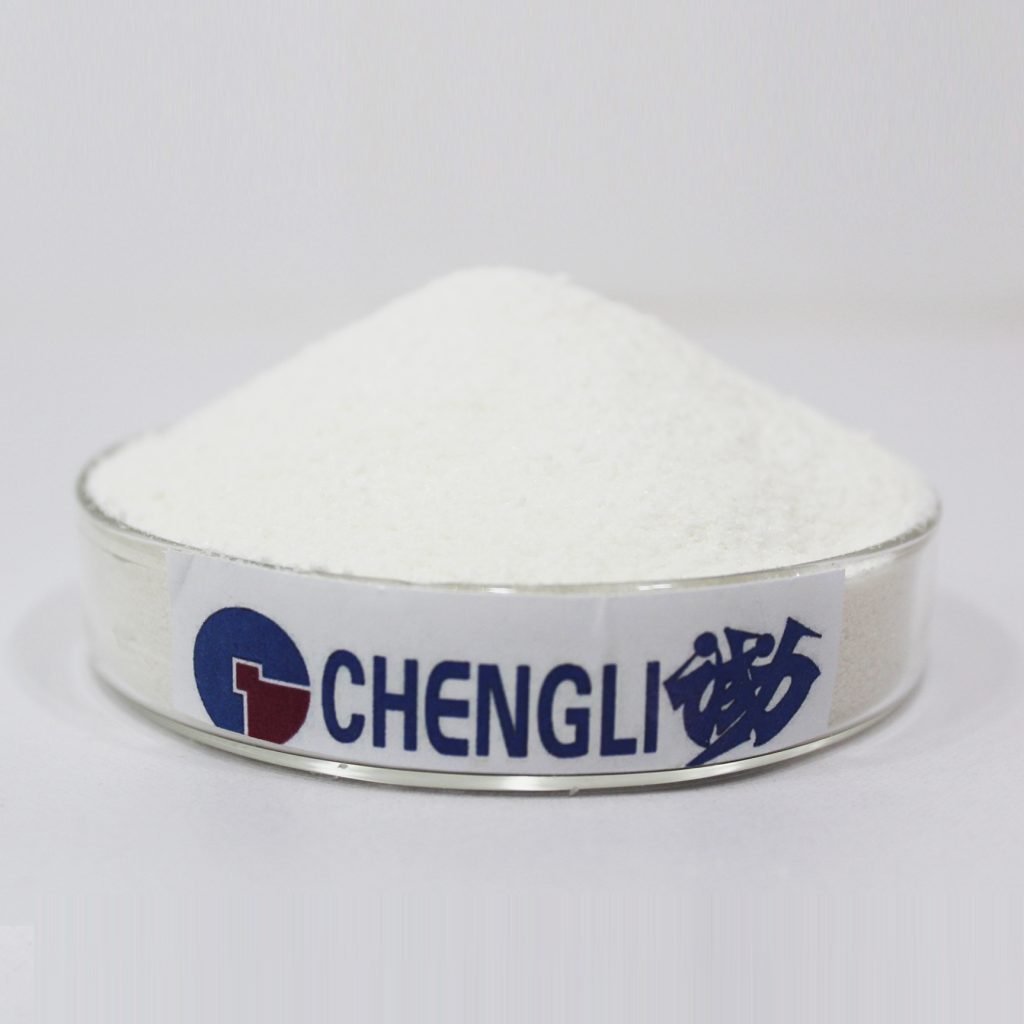
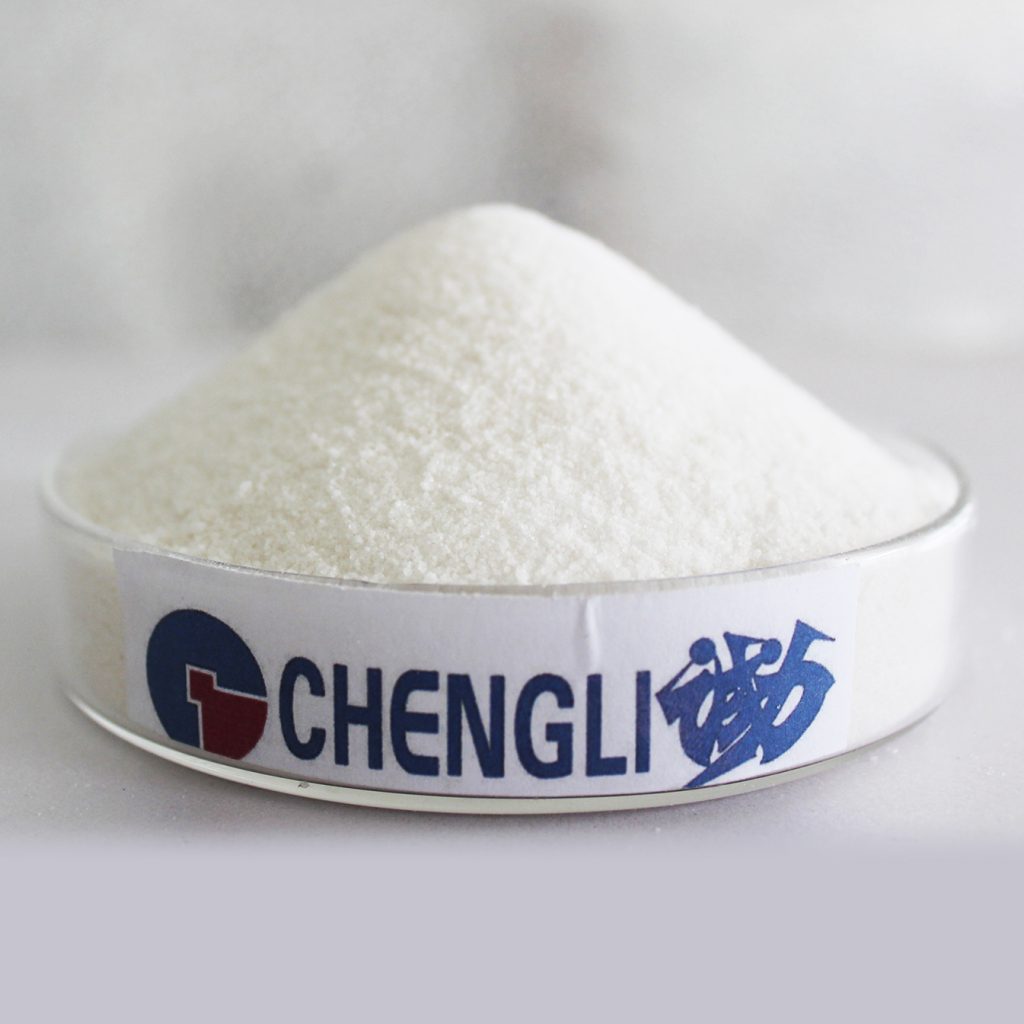
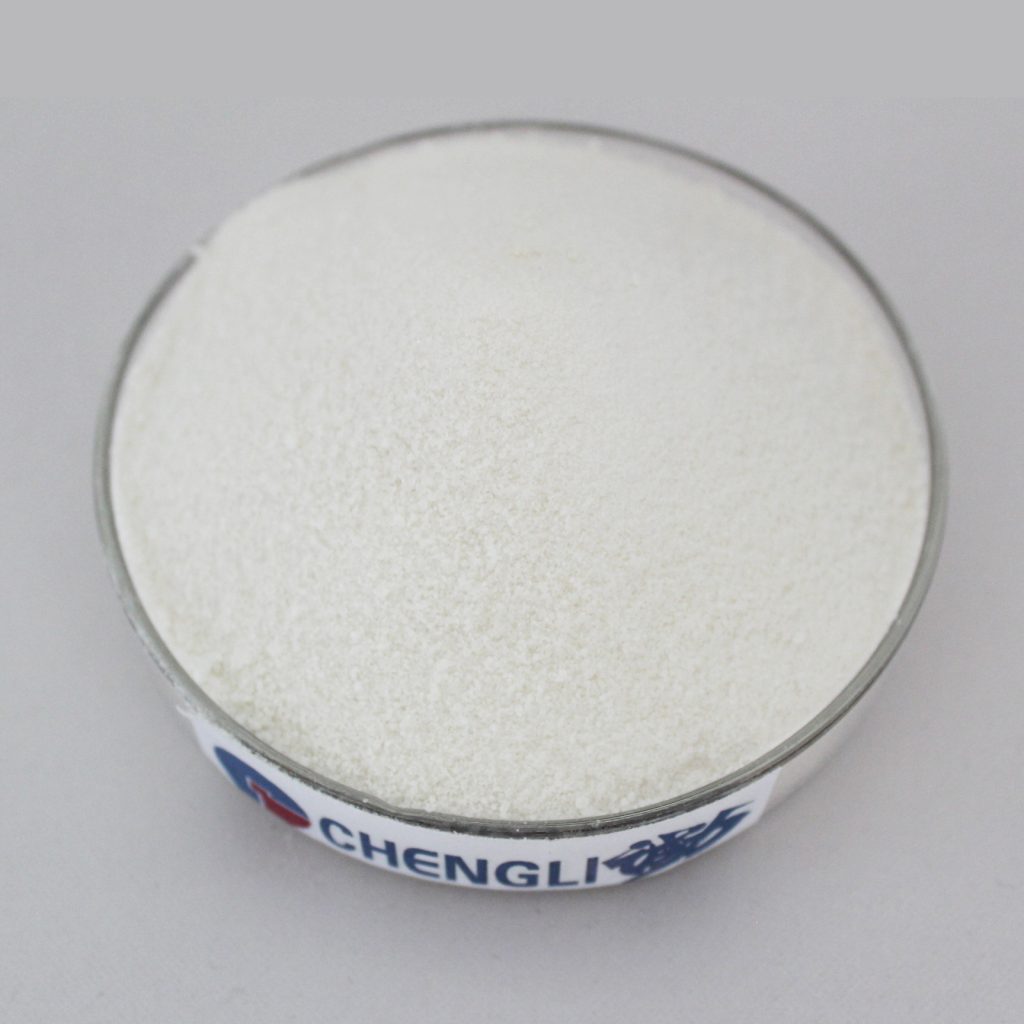
Why Builders Choose It Over Traditional Retarders
Three practical advantages make sodium gluconate a jobsite favorite:
- Micro-Dosing Control: Just 0.1%–0.3% of cement weight tweaks setting time significantly. Need an extra 30 minutes? Adjust the dose without sacrificing final strength.
- Weather Warrior: In scorching heat (where concrete can set in minutes), it prevents rushed work. In cooler temps, it avoids over-retardation.
- Strength Saver: Unlike some additives that weaken concrete, sodium gluconate maintains—and can even boost—long-term durability.
Real-World Impact: Where Precision Matters Most
Application | Challenge | Sodium Gluconate Solution |
---|---|---|
Desert Construction | Rapid setting (<1 hour) | Extends workability to 2–3 hours |
Mega-Pours (dams, bridges) | Cold joints from interrupted pours | Enables continuous multi-hour pours |
Precast Factories | Inconsistent batch setting | Standardizes hardening timelines |
Long-Haul Concrete | Hardening in transit | Keeps mixes workable en route |
Getting the Best Results
Smart use requires attention to four factors:
- Cement Type: Test dosages for your specific blend (Portland, slag, etc.).
- Water Ratio: Higher water content may demand dosage adjustments.
- Additive Mixes: Plays well with plasticizers, but always pre-test combinations.
- Jobsite Conditions: Heat, wind, and humidity all influence performance—seasoned crews factor these in.
What’s Next?
Innovation continues:
- Greener Production: Manufacturers now derive it from corn or sugarcane, cutting carbon footprints.
- Smarter Tech: Early trials pair it with sensors for real-time setting control during pours.
- Nano-Enhancements: Researchers explore particle coatings for even finer tuning.
The Bottom Line
Sodium gluconate has moved from lab curiosity to construction essential because it solves a fundamental problem: concrete’s fickle timeline. From Dubai’s heat to Toronto’s winters, it gives engineers the dial they need to build on schedule—without compromising strength. As projects grow more ambitious, mastering this chemistry isn’t optional; it’s how we lay tomorrow’s foundations today.
Our Professional Technical Team Is Available 24/7 To Address Any Issues You May Encounter While Using Our Products. We Look Forward To Your Cooperation!